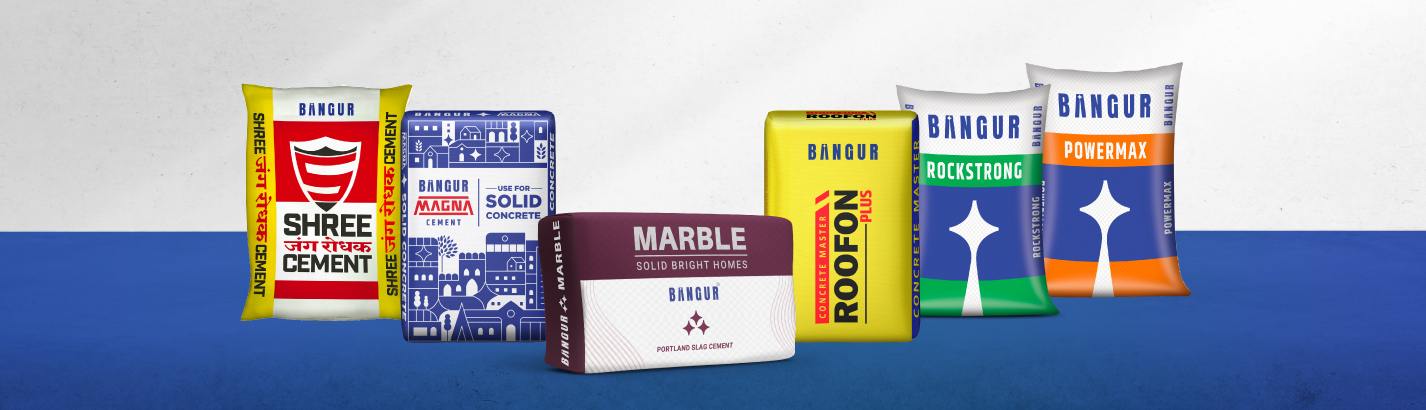
From Gunny Bags to Weather-Resistant Packaging: Reducing Costs of Construction per Square Foot
- Apr 16
- 5 min read
Cement packaging has undergone major transformations through the years to render it tougher and better at keeping the effects of weather at bay. In the beginning, companies put cement in easy-to-use jute sacks. But these sacks had trouble with moisture and ruptured easily. To find a resolution for this, the industry switched from gunny bags to woven polypropylene (PP) sacks. These new sacks were stronger and kept moisture away.
Biaxially Oriented Polypropylene (BOPP) bags and Laminated Polypropylene (PP) sacks help the concrete with better protection from the effects of weather; they are also better at conserving material quality. To demystify how or why the cement industry has transitioned to BOPP bags and PP sacks from gunny jute bags to reduce the cost of construction per sq ft, we need to learn the basics as to why jute bags were used in the first place.
Why has the cement industry stopped using gunny bags for packaging cement for civil construction?
As a natural fiber, the gunny jute bag has been used over the years for packaging cement until they were replaced by better options like polypropylene and weather-resistant packing. Jute fibers offered high tensile strength, which is why gunny bags that are made of jute were considered enough at one time to store and transport cement. Although jute bags are low on generating a carbon footprint and naturally degradable (unlike plastic packaging), they were eventually replaced by better alternatives.
5 Reasons Why Gunny Bags are an Outdated form of Packaging
1. Susceptibility to Moisture
Cement frequently experiences either hardening or degradation while stored or transported under humid or rainy conditions in gunny bags. Gunny bags exhibit fundamental structural vulnerabilities, which become evident from their severe tendency to suffer from moisture damage. Cement reacts dynamically with water interactions while jute functions as a moisture-retaining absorbent.
2. Limited Load Capacity
Jute bags were only capable of transporting small amounts. They were commonly employed for packaging the standard 50 kg bags of cement but were not so strong and efficient for packaging and transporting bulk quantities.
3. Higher Transportation Losses
Due to their weaker resistance to tearing and moisture, jute bags often led to increased material losses during the civil construction logistics process. Cement dust leakage was common, leading to not only financial losses but also environmental pollution and health hazards for workers handling the packaging.
4. Limited Weather Resistance
In contrast to contemporary plastic-yielding cement bags, jute bags were not weather-resistant. Rain or excessive humidity caused the fibers to become brittle and reduced their overall shelf-life. Storage in open or semi-open spaces was therefore extremely risky.
5. Higher Production and Maintenance Costs Over Time
While jute sacks in their initial years were cheap, they were not durable and were going to be replaced relatively more often. Moreover, to prevent dampness, extra linings or coatings had to be applied, contributing to packaging costs in general.
The advantages of upgrading to Biaxially Oriented Polypropylene (BOPP) bags for packaging cement for civil construction
Palleting cement needs water-resistant and strong material that can insulate the material from the environment. BOPP has proven to be a real player in this market with its beautiful attributes. Although the two products contain some merits, they have some vices built into them to be thought about by manufacturers.
1. Superior Strength and Durability:
Because BOPP films are biaxially oriented, they have a higher tensile strength and are more resistant to tearing or punctures. This is especially appropriate for cement packaging, as bags are handled roughly during transportation.
2. Moisture and Chemical Resistance:
Preventing moisture intrusion, which could cause cement to harden too quickly, is one of the most crucial aspects of cement packaging. Even in damp conditions, BOPP's exceptional moisture resistance protects the contents.
3. Enhanced Printability and Aesthetics:
BOPP films provide a glossy surface finish to print, which allows manufacturers to include sophisticated branding, product text, and vivid color. This makes the product more visible and increases marketing opportunities.
4. Lightweight and Cost-Effective:
BOPP packaging is lightweight, which reduces transportation costs. It is also an inexpensive option as it is durable and has less chance of product loss, thereby reducing the cost of construction per sq ft.
The advantages of using Laminated Polypropylene (PP) bags for packaging cement for civil construction
Laminated polypropylene bags are becoming more popular among cement brands due to their exceptional moisture resistance, which keeps cement from hardening too quickly. Compared to traditional jute gunny bags, these bags are more robust, less likely to break during transportation, easier to handle, more affordable at scale, and offer superior branding potential with high-quality printing capabilities.
1. Multi-Layered Protection:
Multiple layers of polypropylene make up laminated PP packaging. The inner layers are built for strength; the outer layers protect from UV light and moisture. Protection from the elements is much enhanced by this layered approach.
2. Excellent Barrier Properties:
Laminated PP bags have rather strong barrier qualities against dust, moisture, and UV light. This function is especially useful for outdoor storage since it is essential to preserve cement from demanding environmental surroundings.
3. Customization and Flexibility:
Laminated PP can be customized to fit specific needs by adding anti-slip components or increasing puncture resistance. Its adaptability makes cement producers especially like this option.
4. Increased Longevity and Reusability:
Laminated PP's strong construction helps it to last, lowering the possibility of damage or tearing during transportation and storage. One great advantage of its durability is its simplicity of reusing.
Why have cement brands shifted from gunny bags to BOPP and PP weather-resistant packaging?
Gunny jute bags were very crucial to cement packaging for decades, offering environmental friendliness, reusability, and cost-effectiveness. However, their vulnerability to moisture, lack of weather resistance, and limited durability made them less suitable for long-term use. Cement usage has transitioned to polypropylene-based bags, which provide high strength, moisture resistance, and cost-effectiveness. Gunny bags have hence been replaced by BOPP and PP bags as the latter offer ample benefits with regards to cement packaging, guaranteeing strength, moisture resistance, and durability.