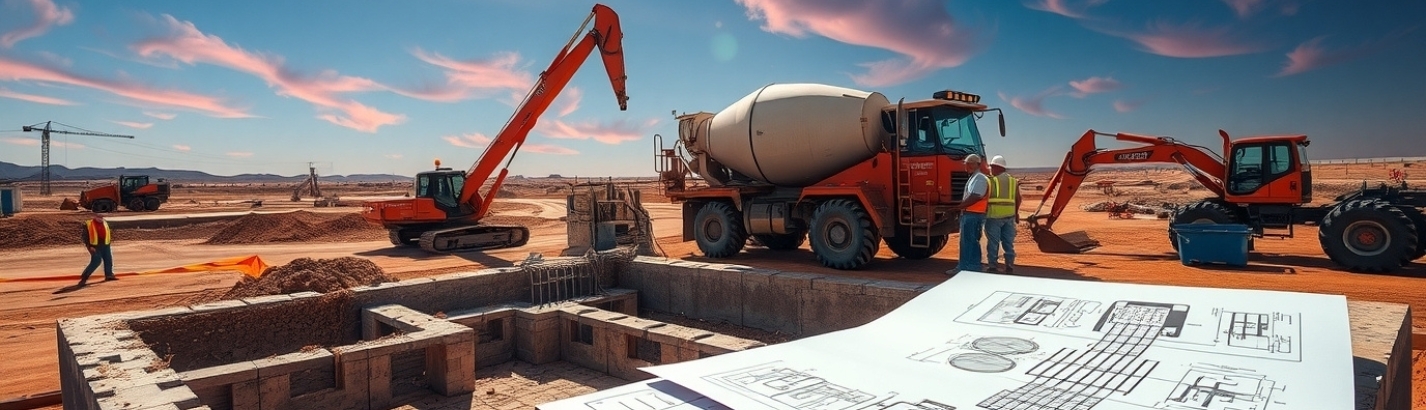
Building Construction Step-by-Step: From Site Prep to Bulk Cement Orders – Your Complete Guide
- Jul 2
- 7 min read
Building a home or any structure is always about getting the basics right. From clearing the land and setting foundations to choosing the right type of cement and managing the site, every step is important. This blog simplifies the full process of building construction, explains what materials to use where, and helps you avoid common mistakes.
Key Takeaways
Good construction starts with good planning — soil tests, clear layouts, and proper approvals.
Each step builds on the last, and early mistakes can cost you later.
Use the right cement in the right place — structure vs finish makes a difference.
Don’t rush a bulk cement order because timing and storage matter.
A neat, well-managed construction site keeps the build on track.
Finishing touches aren’t minor — they decide how your home feels in the end.
Building construction isn’t just about stacking bricks or pouring concrete. It’s a process where every stage affects the next and mistakes made early on during the process can show up years later. Whether you're building a home or just trying to understand how things work,, this guide breaks down the complete process with a focus on practicality and long-term quality.
Step 1: Choosing and Preparing the Plot
Every building construction starts with choosing the right plot. The foremost thing to keep in mind before buying a plot is the quality of soil beneath the land. A simple soil test determines the results and can tell you how deep and strong your foundation needs to be. Besides that it is also necessary to check for legal clearance, accessibility, and availability of basic amenities like water and electricity.
Once the plot is finalised, the construction site must be cleared, levelled, and marked as per the layout plan. Trees, rocks, and debris are removed. The soil is compacted, and ground levels are verified.
Step 2: Planning and Approvals
You can’t build without a plan. And you definitely can’t build without approvals. This stage involves working with architects and engineers to prepare:
Floor plans and elevations
Structural drawings
Plumbing and electrical layouts
These drawings are then submitted for government approvals. Once cleared, the execution begins.
Step 3: Foundation Work
This is where your building under construction takes its first real shape. Excavation is done as per the structural plan, followed by a layer of PCC (plain cement concrete). Steel reinforcements are placed, and footings are cast using concrete.
Proper curing is essential at this stage. It's what keeps the structure from developing cracks or becoming unstable over time.
Step 4: Raising the Superstructure
This is where most of the structural work happens. Columns are cast first, followed by beams and slabs. Floor by floor, your home begins to rise. This is a key phase in civil construction where the frame of your building is created.
Each slab must be cured thoroughly, and vibration during casting must not be skipped as it ensures concrete spreads evenly and no air gaps remain.
Step 5: Wall Construction and Room Layout
Now, the walls are built. Bricks or blocks are laid, thus forming the internal rooms and external boundaries. Openings for windows and doors are created, and lintels are placed to hold weight above them.
This stage shapes your home. A good mason will ensure uniform joint thickness, alignment, and wall heights that match the plan precisely.
Step 6: Waterproofing and Roofing
The roof slab is cast once the top floor walls are done. But before you move forward, waterproofing treatments are applied not just on the terrace, but also in bathrooms, balconies, and utility areas. It’s much harder and costlier to fix leakage issues once tiles are laid and interiors are done.
Step 7: Internal Utilities — Pipes, Wiring, and More
This is the ‘invisible’ part of building construction and also one of the most important. Electrical conduits, water supply lines, drainpipes, and gas lines are installed before plastering.
Testing is crucial here. Any leakage, block, or wiring fault caught early can save a lot of rework later.
Step 8: Plastering and Frame Fittings
Plastering smooths the walls and readies them for paint. It also covers up wiring and pipework installed earlier. Once plastering is done, door and window frames are fitted. Sealing around these areas helps prevent air or water seepage.
Step 9: Flooring, Tiles, and Surface Finishes
Different rooms call for different materials like anti-skid tiles for bathrooms, vitrified tiles in living areas, and granite in staircases and counters. Wall tiling is done in bathrooms and kitchens before painting begins.
After tiling and final curing, surfaces are prepared with putty and primer. Then, paint is applied in the chosen shades.
Step 10: Finishing Fixtures and Fittings
Now come the finishing touches:
Bathroom fittings: taps, shower heads, flushes
Electrical fixtures: fans, lights, switches
Modular furniture, cabinets, and wardrobes
Railings, grills, water tanks, and solar units
These are installed as per design and everything is tested to make sure it works properly.
Final Inspection and Handover
Once all work is complete, a thorough inspection is a must. Go room by room and check:
Plumbing and drainage lines
Electrical points and fittings
Window and door alignment
Paint finish, tile levelling, and sealants
Only when everything checks out should you move forward with handover and possession.
Now that you have a basic understanding of the steps that a construction process goes through, here are a couple of tips that may yield better results:
Cement Tips: Choosing Smart and Buying Right
No matter how good your layout or labour, if the cement fails, everything suffers. Choosing the best cement for house construction means understanding where and how you’re using it.
OPC cement is usually preferred for its quick setting time, high strength and durability.
PPC offers superior finish, is crack-resistant and also gains strength over time, thus ensuring long-lasting durability.
When working on a large project, placing a bulk cement order can help you save money and offer consistent quality. But you must also remember that cement doesn’t last forever, so it should be used within 90 days of manufacture and kept away from moisture.
Pro Tip: Plan your purchases in 2–3 stages across the project timeline to avoid waste and ensure freshness.
Managing Materials on Site
Handling construction and building materials isn’t just about stocking them but it’s about using them correctly and here are some key pointers:
Cement should be stored on raised platforms in dry areas
Sand and aggregates must be kept separate
Bricks should be stacked to avoid breakage
Steel should be covered to avoid rusting
A clean, well-organised construction site improves workflow, reduces errors, and avoids unnecessary delays.
Final Word
There’s no shortcut to quality in building construction. Every step has its own importance from soil testing to plastering, from choosing the best cement for construction to managing your bulk cement order without wastage.
If things are done in the right way, the effort you put in during construction will reflect in the way your home feels, not just today, but for years to come.
FAQs
What is the step-by-step process for building construction?
The different steps of building construction are as follows:
i) Design and Planning
ii) Securing necessary permits
iii) Site Preparation
iv) Laying the Foundation
v) Building the Superstructure
vi) Roofing
vii) Plumbing and Electrical works
viii) Interior and Exterior finishing
ix) Final Handover
What are the 4 main types of construction?
The four main types of construction are, Residential, Commercial, Industrial, and Infrastructure.
Which cement is best for building?
OPC cement is usually considered as the go-to choice for building projects, but depending upon construction requirements or environmental factors, other types such as PPC or PSC cement are also used.